The Importance of Following Product and Plant Standards
SIGMA prioritizes the safety of your operations and products
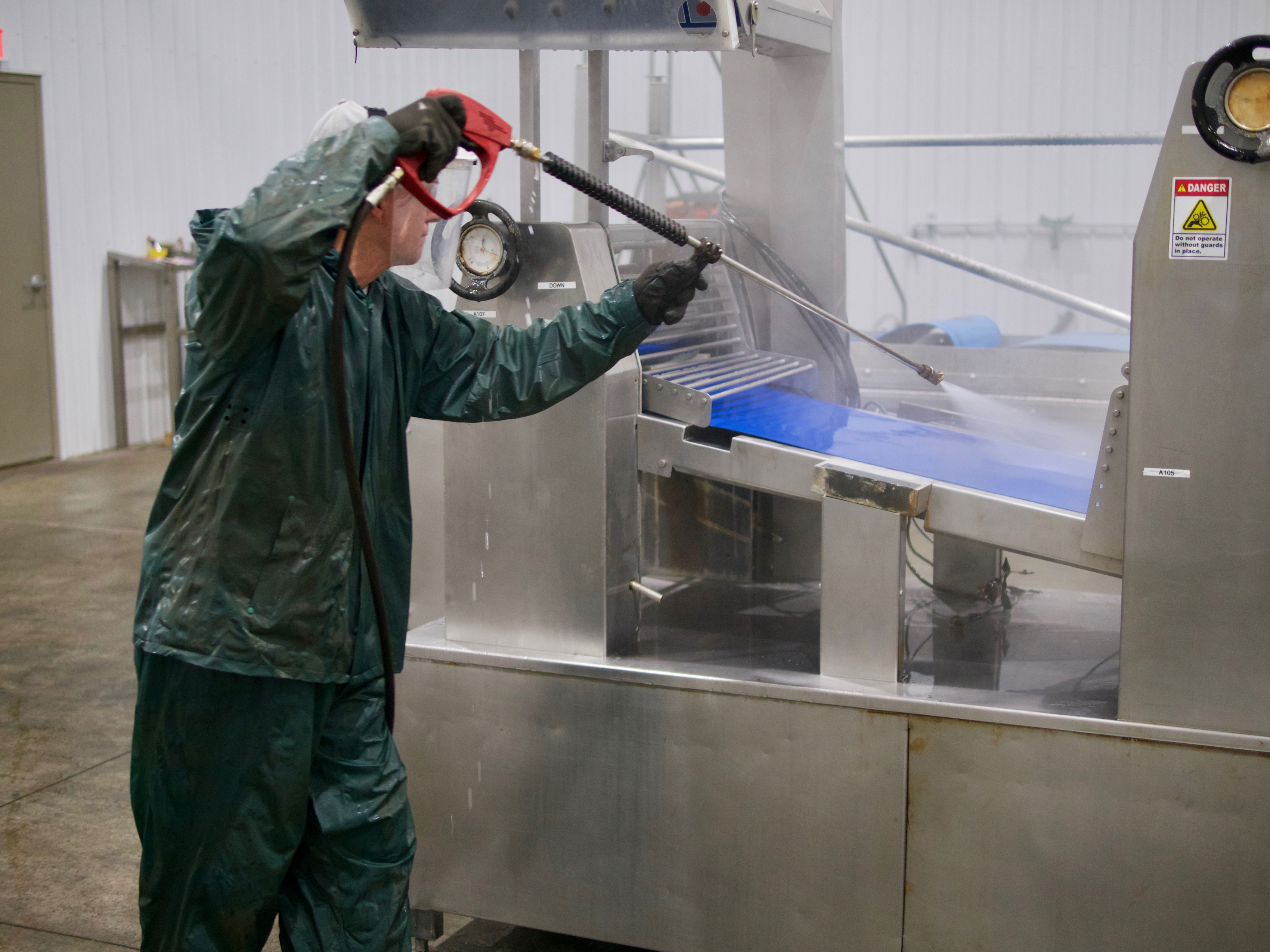
SIGMA Equipment sells a wide variety of new and used packaging and processing equipment and works closely with numerous industries. Specifically, when working with pharmaceutical, food, and beverage industries, product and plant safety, and quality regulations must be strictly adhered to and held to the highest standards.
We know how important safety, quality, and brand reputation are to our clients. Appropriate steps and daily measures must be taken to ensure safety and quality for not only a company’s operators, but for their products and customers as well.
Why are product and plant standards important?
When buying packaging or processing equipment, you must take care to ensure that it is properly inspected and is in working condition. Any faults in your equipment or machines can lead to quality issues, production downtime, and workplace injuries.
What to look for when inspecting equipment
When inspecting equipment for purchase, you should always make sure your equipment is safe for operators and production. Below are some items to pay close attention to when inspecting equipment. These will help you determine if the machine is safe for your employees to operate as well as produce quality products.
- Does the machinery have sufficient guarding and safeties?
- An example of this is emergency stops.
- Any evidence of a weld repair?
- Are there any exposed pinch points?
- Any signs of rust or corrosion?
- Is the paint chipping?
- Is the equipment wash-down rated?
- Are there cracks or chips in the lexan guarding?
- Are there areas where bacteria can collect?
- Evidence of harbrige points, rodent or insect infestation?
- What was the last product run on the machine?
Equipment standards
Not all plants or equipment have the same standards. Often, the level of inspection and scrutiny that a machine will face will depend on what industry you are working in.
- Pharmaceutical - this industry holds plant quality and safety standards to the highest level and will always need to assure their machines are working and sanitized properly.
- Food and beverage - any facility processing products such as raw meats, dairy, fresh fruits, and vegetables typically perform daily inspections of their equipment. Plants that are free of a particular allergen (including gluten-free, kosher, etc.) should also be inspected regularly.
Another element that factors into the level of inspection a machine will undergo before production is the location of the machinery in a production line. For example, a machine that’s in the processing or filling (food contact) area will be scrutinized much more closely than a machine that’s in packaging or other non-food contact areas. Often these machines are swabbed to test for proper sanitary conditions at the micro-biological level. This is to maintain the safety and quality of food products during the production process.
Inspections
A company's quality assurance and safety teams should scrutinize new processing machinery at a higher level than any other inspector. The function of a company's internal quality assurance team is to ensure that regulatory standards are being met or exceeded at all times so that safe quality food is being produced. Furthermore, quality assurance teams assist production by auditing machinery on a consistent frequency to ensure that a plant meets regulatory standards all year round.
In addition to internal standards, there are also external regulatory agency standards that companies must follow. One of these is the US Department of Agriculture (USDA). This Food Safety Inspection Service inspects food plants daily and has the authority to stop production if regulatory standards are not being upheld. Some other regulatory agencies include:
- USDA
- FSIS
- MPI
- FDA
- OSHA
Regulatory agencies provide a secondary audit to ensure that companies as a whole are functioning within regulation specifications. All regulatory agencies can audit as they see fit, so it is better to uphold the standard of “audit ready” at all times.
Sanitization before production
Before production, a plant that follows USDA regulations will perform a sanitation cycle the following tasks on machinery that consists of the following:
1. Physically remove product debris from equipment.
2. Rinse equipment with hot water to remove any remaining debris.
3. Apply an approved cleaner to the equipment either by foaming or soaking.
4. Rinse the equipment once more with hot water.
5. Reassemble the machinery.
Summary
Following product and plant standards are so important to SIGMA because they give us a better understanding of our clients’ expectations and what standards they may have when looking for machinery. Knowing the standards for a certain industry helps us understand if a machine will be a good fit or provide value to a customer.
To learn more about how we take product and plant standards into account when working with customers and the equipment we sell, get in touch with one of our equipment experts today.